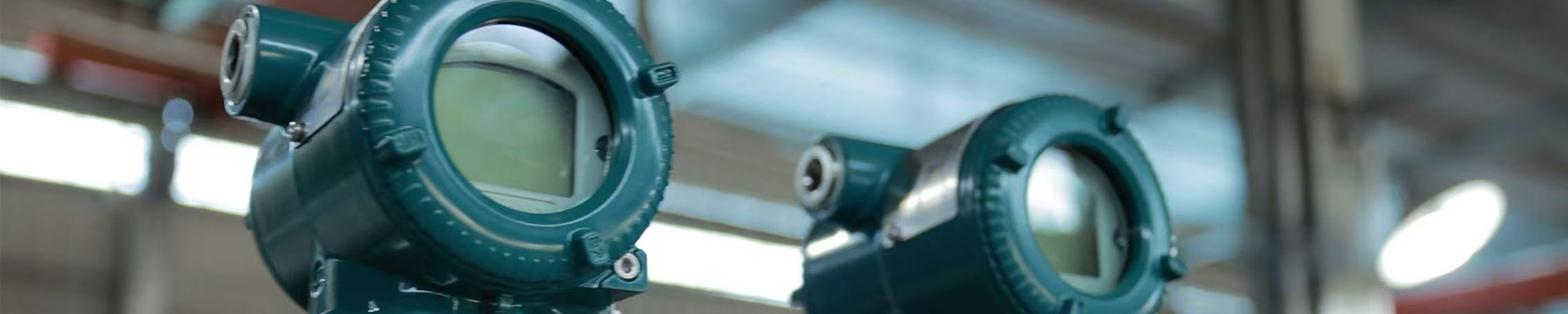
Global Industrial Equipment Embraces Modular Revolution, Multi-scenario Solutions Drive Intelligent Industrial Transformation
2025-05-17 17:28Against the backdrop of the accelerated intelligent upgrade of the global manufacturing industry, the matrix of modular equipment led by skid modules is triggering a new round of industrial revolution. Recently, the standardized module series displayed at an international industrial equipment exhibition, with its breakthrough integrated design concept, has provided a new paradigm for equipment upgrades in fields such as petrochemicals and energy power.
The skid module, as the core unit, adopts an aerospace-grade aluminum alloy frame. Its compact specification of not only reduces transportation costs by 42%, but also enables system reconfiguration to be completed within 72 hours through patented quick-disconnect interfaces. The accompanying surge relief skid, equipped with intelligent pressure sensing chips, can monitor pressure fluctuations at the 0.01MPa level in real time, and has successfully reduced the system failure rate to below 0.3% in high-pressure scenarios such as LNG transportation.
In the field of thermal management, the temperature and pressure reducing device innovatively adopts a three-stage buffering structure, and in combination with the steam pressure reducing module's nanocoating technology, the energy efficiency conversion rate of high-temperature steam systems is increased to 92%. After a chemical company applied this combination of modules, its annual maintenance costs were sharply reduced by 2.8 million yuan, and equipment downtime was shortened by 76%.
The modular trend in energy equipment is particularly significant in the gas field. In the dual-specification gas pressure regulating skid series, the basic model meets the needs of urban gas pipeline networks, while the 800 * 800 enhanced module is designed specifically for LNG receiving stations. Its redundant safety valve group can achieve emergency shut-off at the 0.5-second level. The accompanying skid-mounted LNG module, which adopts double-layer vacuum insulation technology, has a BOG recovery efficiency of 98%, helping a coastal storage and transportation base reduce CO2 emissions by 12,000 tons per year.
On the equipment manufacturing side, the modular production mode of stainless steel pressure containers has attracted industry attention. Through the cluster operation of laser welding robots, the production cycle of the standard container is compressed from 45 days to 12 days, and the weld seam qualification rate is stably maintained at above 99.97%. The prefabricated pipeline system, using BIM modeling for prefabrication, has increased the pipeline installation efficiency of a refinery expansion project by three times and controlled the material loss rate within 1.8%.
Industry analysts point out that this "Lego-style" modular equipment ecosystem is reshaping the industrial manufacturing landscape. It is expected that by 2028, the global market size of modular pressure vessels will exceed 24 billion US dollars, with the Asia-Pacific region accounting for more than 45%.