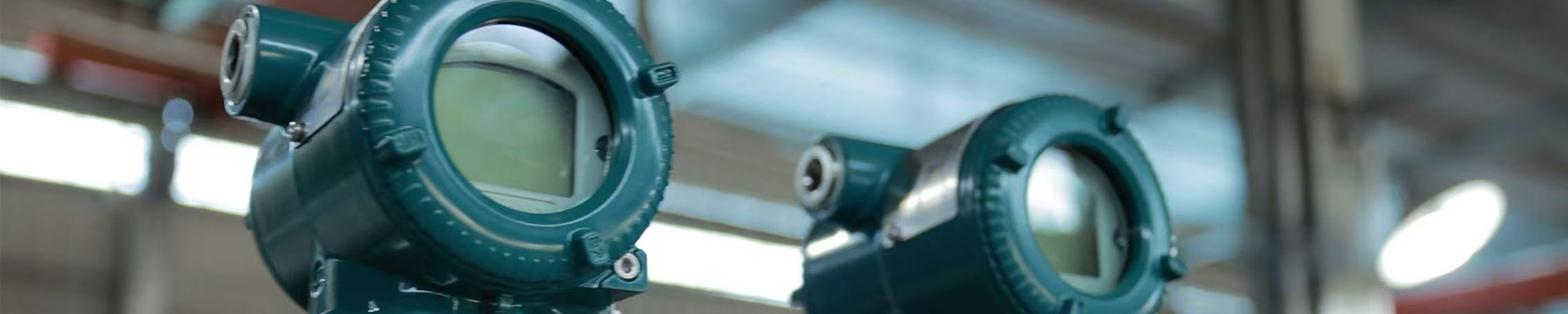
Modular Equipment Clusters Break Technical Boundaries, Intelligent Manufacturing Kicks Off the New Era of Industry 4.0
2025-05-17 17:31At the latest technology release event of the Hannover Messe in Germany, the fourth-generation modular industrial equipment jointly developed by multinational companies caused a sensation. While maintaining the golden size of , the series of products has realized intelligent collaboration of equipment clusters through IoT technology innovation, marking the formal entry of industrial equipment into the evolutionary era.
The skid module, as the "cell unit" of the smart factory, has now integrated an edge computing gateway. After a car manufacturer deployed 200 sets of this module, it achieved millisecond-level interaction of equipment status through self-organizing network protocols, increasing the switching efficiency of the stamping production line by 60%. The linked surge relief skid, equipped with deep learning algorithms, can predict more than 92% of pressure anomalies and has set a new industry record of 680 days of continuous safe operation in semiconductor special gas conveying systems.
The intelligent breakthrough of the thermal management system is remarkable. The temperature and pressure reducing device and the steam pressure reducing module form a digital twin, optimizing parameters in real time through 3D fluid simulation. After a biopharmaceutical company applied this solution, the steam consumption in the sterilization process was reduced by 37%, and the temperature fluctuation range was controlled within ±0.5℃.
The technological iteration of energy modules is also rapid. The gas pressure regulating skid has added hydrogen energy adaptation functions, and its ceramic composite material valve core can withstand a hydrogen concentration environment of 70%, helping a hydrogen energy park achieve equipment reuse and transformation. The skid-mounted LNG module has introduced a low-temperature latent heat recovery system, reducing BOG treatment energy consumption by 54% and promoting the industry's progress towards zero-emission goals.
In the field of materials engineering, the stainless steel pressure container has adopted gradient composite steel plate technology, increasing its resistance to hydrogen sulfide corrosion by 8 times. The prefabricated pipeline system has innovatively applied graphene coating, reducing the friction coefficient to 0.01 and lowering the pumping energy consumption of a long-distance pipeline by 22%.
It is worth noting that modular equipment clusters have begun to build the infrastructure for the industrial metaverse. A multinational group has used digital thread technology to map the full life cycle data of pressure vessels to physical entities in real time, achieving a breakthrough in predictive maintenance accuracy of 91%. Industry experts predict that this "physical-digital" dual-mode equipment will become the core carrier of the industrial Internet of Things in the next decade.
Get the latest price? We'll respond as soon as possible(within 12 hours)